This website uses cookies so that we can provide you with the best user experience possible. Cookie information is stored in your browser and performs functions such as recognising you when you return to our website and helping our team to understand which sections of the website you find most interesting and useful.
IoT Device Development for Oil & Gas Sensors
Backstory
Sensors are used in the oil and gas industry to monitor equipment conditions.
Measuring instruments must be highly accurate, safe to use, and highly reliable to operate in harsh environments.
High-precision sensors are vital to the industry, as oil is a valuable commodity.
Oil and gas production facilities are places of increased danger due to the high combustibility of these natural resources. That is why monitoring the state of oil and gas equipment is mandatory.
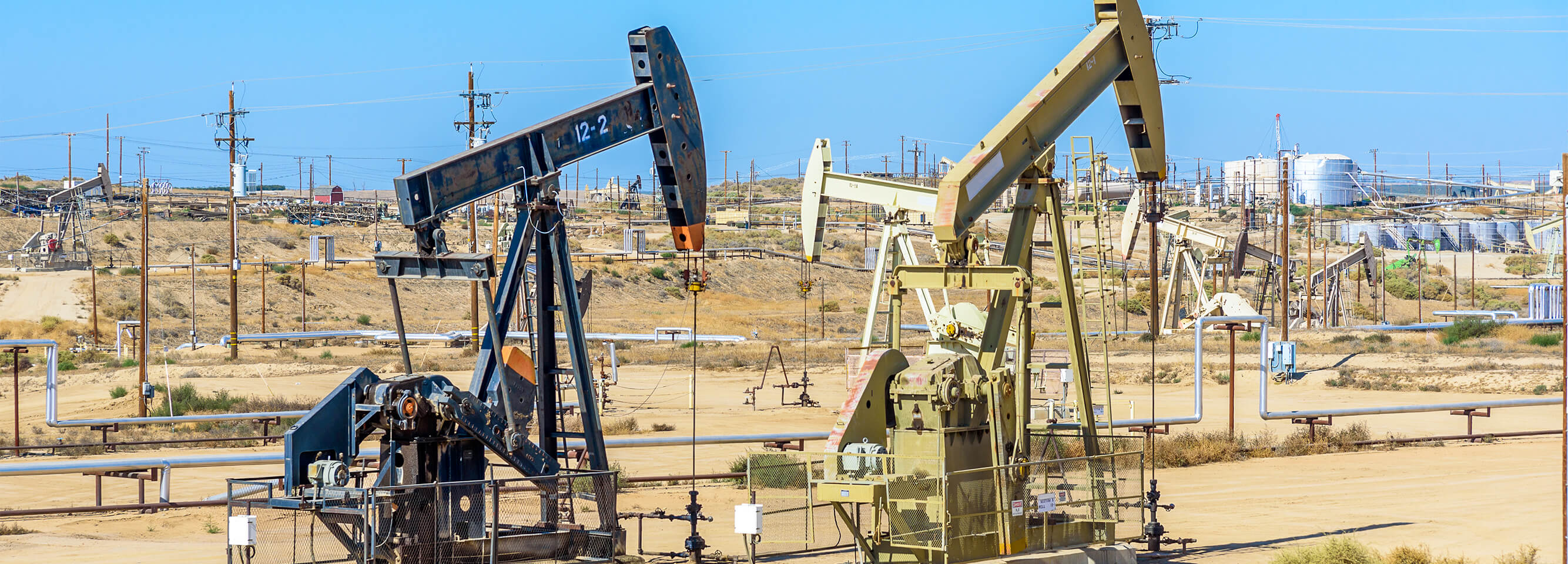
Request
A US company needed to develop an IoT device that could connect to sensors and monitor the status of an oil production facility, pipelines, and oil tanks.
An IoT device for oil and gas sensors should have a cellular module, an internal cellular antenna, and a built-in accelerometer. The connected gadget must be able to receive data from analog (4-20mA/0-10V) and digital (RS-485) sensors.
Neodymium magnets should provide reliable device adhesion to various surfaces.
The device must be powered and charged using a solar panel and a battery of suitable capacity.
The project's overarching goal is to develop an IoT device for oil and gas sensors and an AWS-based backend. We have developed IoT hardware, firmware, and a backend for API debugging.
The device has several options for use.
First, the IoT solution is used to determine the operation of pumpjacks, so it has a built-in accelerometer. The gadget is attached to the pumpjack with high-strength rare earth magnets.
The embedded tilt and vibration sensor detects equipment vibrations, allowing specialists to monitor the pump operation remotely and fix downtime and breakdowns.
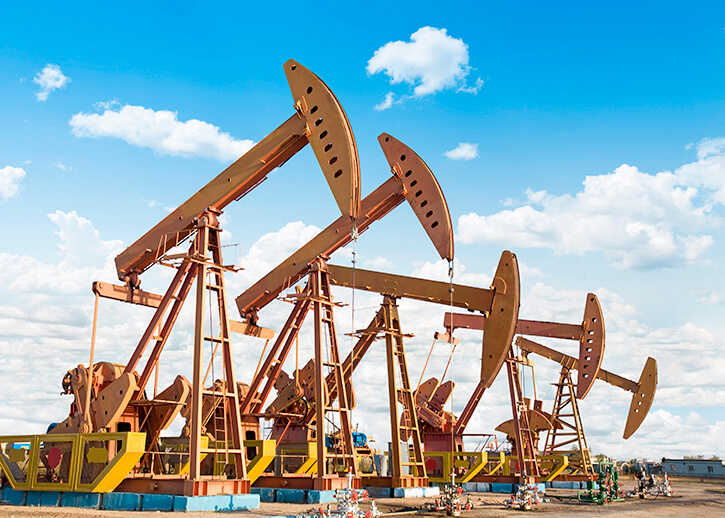
Secondly, the IoT object determines the oil level in tanks.
The device has industrial interfaces for pressure, liquid height, and other analog sensors (4-20 mA / 0-10 V) or digital RS-485. It also has a low-noise, high-gain sensor signal amplifier for signal processing.
The third use case is to connect the device to an external pressure sensor installed in a pipe to monitor the pressure inside it and ensure the absence of breaks.
The nRF9160 module used in the PCB design has a built-in GPS receiver, enabling users to know the device's location by getting its coordinates.
The IoT solution does not require an external power source.
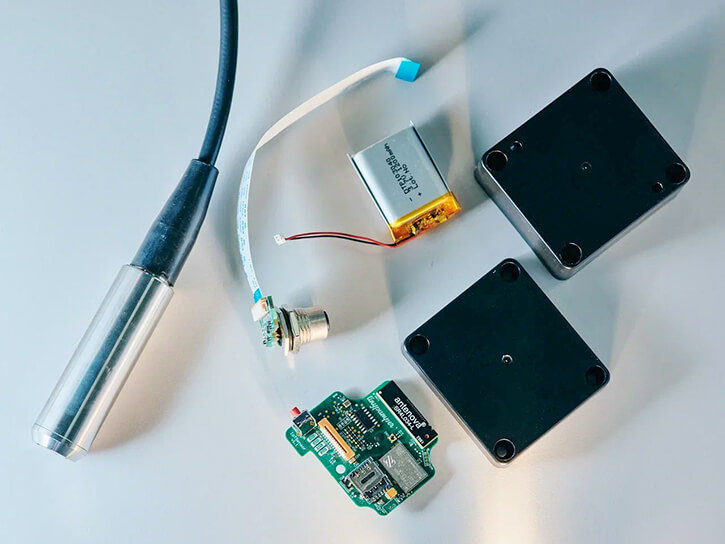
Solar panels are installed on the gadget case to power and charge the internal battery. Thus, the device can work 24/7. The solar panel charges the battery and powers IoT during the day, and the battery drives the gadget at night.
We chose a high-capacity custom rechargeable battery with fault protection circuitry for stable device operation.
A cellular module with a cellular antenna provides device communication and allows it to send the received data in JSON format via HTTP requests to the AWS cloud.
We have set up the Amazon service to collect and view JSON data sent from devices to check and debug devices according to the collected data.
Users can view the gathered data using a standard Amazon viewer with no GUI provided.
The device is designed according to general restrictions for hazardous environments (without arcs, sparks, and excessive heating during work) to comply with certification rules.
Our specialists used FCC- and CE-certified modules for a streamlined certification process. The system is also prepared for Class 1/ Div 1 and Div 2 certification, which regulates hardware operation in explosive environments.
We provided all the necessary documents and prototypes, including a PCB design, a list of components used, and design solutions with a case for passing a certification.
Major Issues Resolved
A challenge related to PCB design was to create a board that would fit the size of the factory case approved by the customer.
In the final version, the device has two printed circuit boards. A 6-layer high density PCB with a processor and all the components is placed at the bottom of the case. A PCB with a connector for external sensors is located on the side face.
The second issue was to ensure the energy balance so that the device could work with a constant recharge during daylight and operate on a battery charge during dark hours.
The IoT solution is constantly recharged from a solar battery during daylight using a specialized microcircuit. The high-capacity battery ensures stable device operation at night.
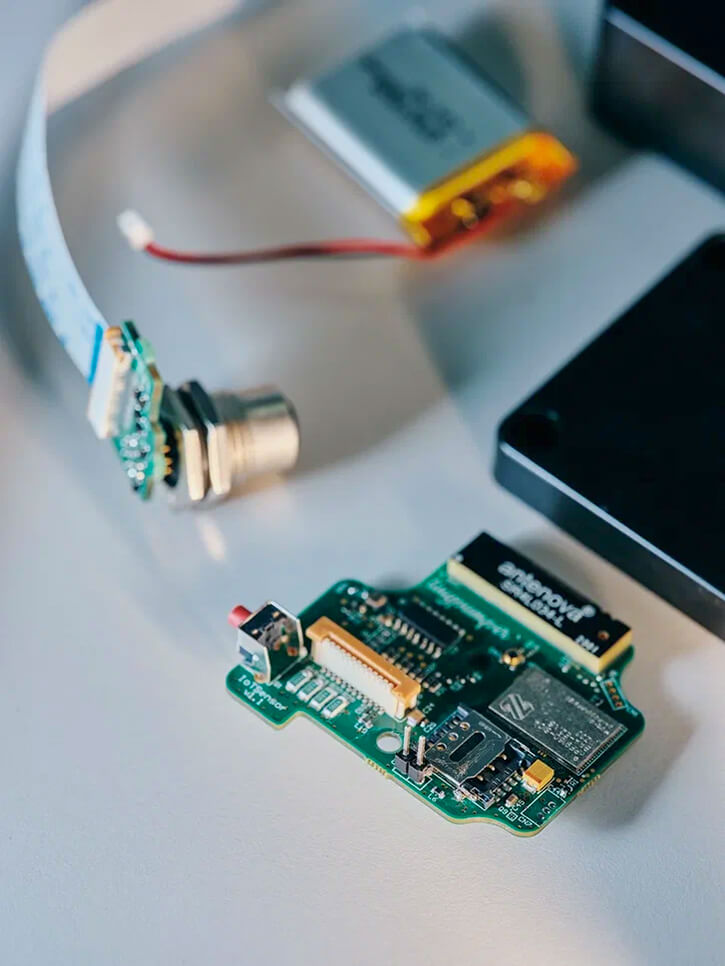
Scope of Work
- Schematic and PCB design
- PCB assembly, testing, and fixing
- Firmware development
- Web development
Technologies Used
- We used Altium Designer for schematics and PCB design.
- Custom firmware is written in С/C++ using the Eclipse IDE.
- We used a small, scalable, real-time Zephyr RTOS optimized for resource-constrained devices.
- We chose a compact, highly integrated, low-power nRF9160-SICA-R7 System-in-Package (SiP) with an integrated LTE-M/NB-IoT modem and GNSS.
- LED indicators point out the operating mode.
Result
Our hard work resulted in the creation of an IoT system for oil and gas production equipment.
The built-in accelerometer allows the device to track the tilt and vibration of the pumping unit to account for its operating time.
By receiving data from external pressure sensors installed on the pipeline and temperature and liquid level sensors located on oil tanks, the gadgets allow personnel to monitor the state of the oil and gas infrastructure.
The device was built taking into account all the US and EU requirements regarding hardware operation in an explosive atmosphere and is ready for certification.
The IoT system helps increase oil and gas facility safety and efficiency.
You might also like...
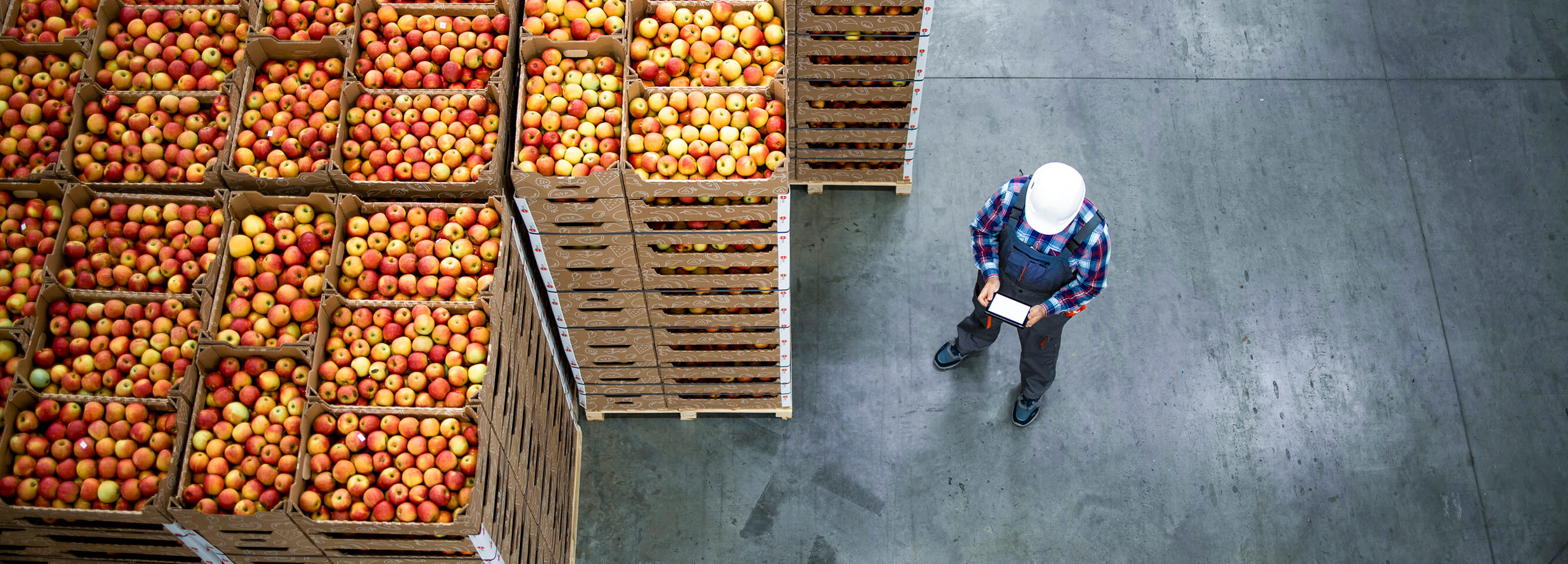
Temperature and Humidity Monitoring System for Warehouses
The system consists of sensors, central hubs, a cloud and a mobile application. It monitors indoor parameters in real time and sends notifications to the users if the values exceed the allowed limits.
LEARN MORE
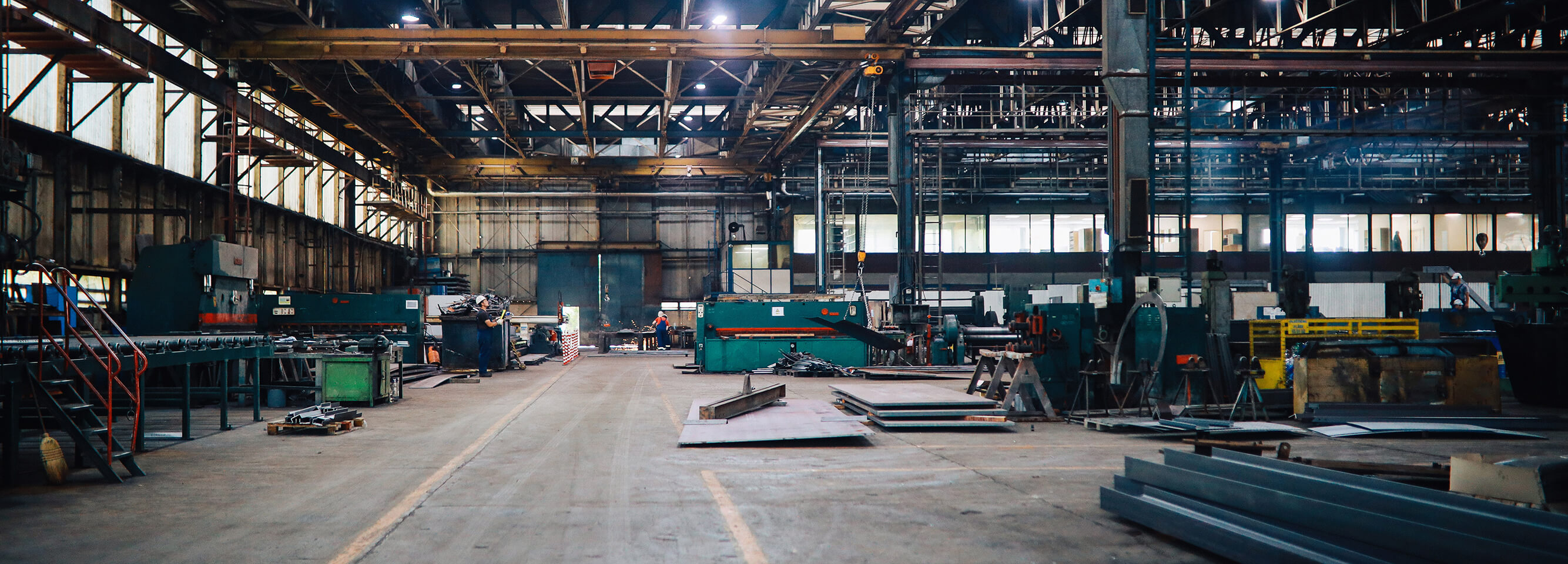
Industrial Emergency Detection System
The solution uses artificial intelligence to process images from IP cameras, detect dangerous incidents, and send an alarm to a Jmix application.
LEARN MORE