This website uses cookies so that we can provide you with the best user experience possible. Cookie information is stored in your browser and performs functions such as recognising you when you return to our website and helping our team to understand which sections of the website you find most interesting and useful.
Hardware Development for Industrial Solutions: Popular Technologies, Design Techniques, and Requirements
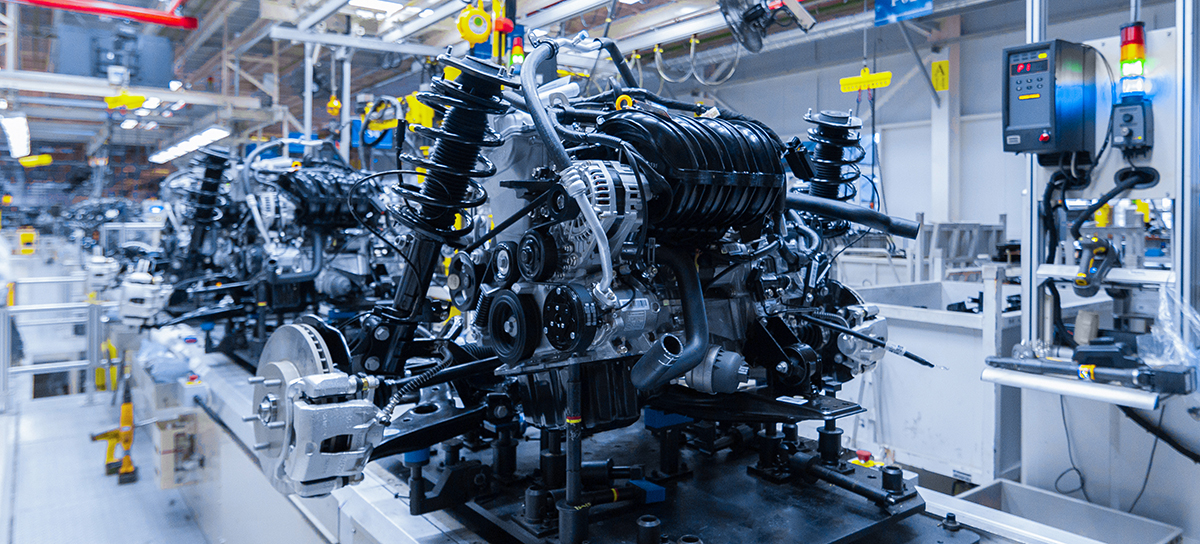
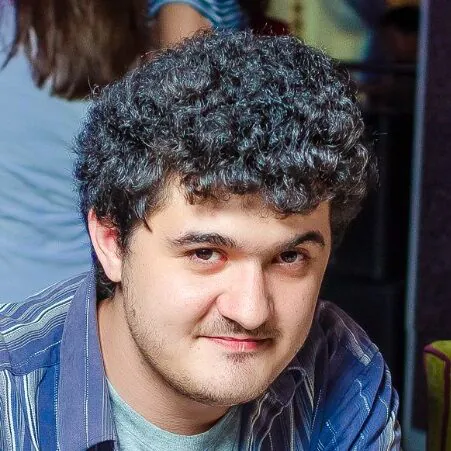
Timur Yuldashev
IT Writer, PhD in Philological Sciences
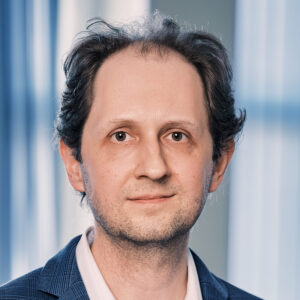
Andrey Solovev
Chief Technology Officer, PhD in Physics and Mathematics
- What is Industrial Electronics?
- Consumer vs Industrial Hardware Development
- Popular Industrial Electronics Solutions
- Information Required for Industrial Hardware Development
- Certification and Testing
- Integra Source’s Experience in Industrial Hardware Design
- Vibration Conditioning Device
- People Tracking Device for Mining Industry
- Customizable Asset Tracking Platform
- Conclusion
One can see many electrical devices in the consumer sector. Businesses use electronics too: payment transactions, monitoring systems, smart advertising, etc. What common people rarely see is how often high-tech electronics are used in manufacturing. In this article, we are going to discuss hardware development for industrial solutions. We will talk about the differences between consumer and industrial electronics design and the requirements for industrial-grade hardware. We will also discuss some of our industrial projects.
- What is Industrial Electronics?
- Consumer vs Industrial Hardware Development
- Popular Industrial Electronics Solutions
- Information Required for Industrial Hardware Development
- Certification and Testing
- Integra Source’s Experience in Industrial Hardware Design
- Vibration Conditioning Device
- People Tracking Device for Mining Industry
- Customizable Asset Tracking Platform
- Conclusion
What is Industrial Electronics?
Industrial electronics refers to electronic devices and systems used for manufacturing goods. They cover a wider range of machines, components, and system elements that participate in the production of goods: power electronics and converters, electrical machinery, motor drives, etc. Such devices include control systems, sensors and measurement systems, communication and industrial automation solutions, and more.
Devices for industrial purposes are designed according to the same basic principles as consumer or commercial electronics. However, there are crucial differences as well. Our team has participated in industrial projects before, so we know about the strict requirements for this type of hardware. We can help with your project too. Contact us to discuss the details.
Consumer vs Industrial Hardware Development
When designing consumer electronics, the engineers’ first priority is to make the device as affordable as possible and start production as soon as they can. Other factors are of secondary importance. In industrial embedded hardware design, reliability is the most important factor. Here are the key features of industrial electronics development.
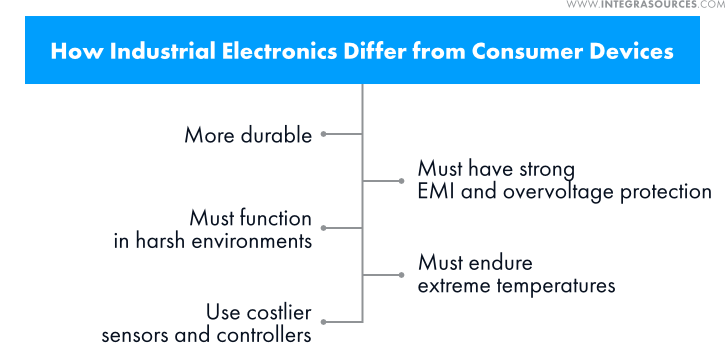
- Reliability
People regard many consumer-grade devices as durable. However, rebooting your PC or booking a service call is not uncommon. In the consumer sector, affordability is the highest priority.
But if industrial equipment fails, it can disrupt the work of the whole production line. The financial losses can exceed the cost of the equipment. For the same reason, industrial devices are expected to work for much longer without repair. This dictates a different design approach: the choice of better materials, higher-grade components for the PCBs, more durable coatings, etc. It also makes industrial hardware development more expensive.
- EMI and overvoltage protection
When designing consumer electronics, engineers provide devices with a certain level of EMI protection. But technologies we use in everyday life rarely face high levels of noise. Unlike them, the power supply circuits in industrial hardware must be designed in such a way as to suppress strong electromagnetic noise. Electronics used for industrial applications must also have higher overload capacity. Hence the need for additional EMI and overvoltage protection, which adds to the board’s cost.
- Environmental hazards
Equipment used in manufacturing usually functions in harsh environmental conditions: vibration, physical shock, high or low temperatures, humidity, dust, chemicals, etc. To provide protection, engineers make boards thicker, use specific PCB geometries, install vibration dampers, coolers, and heaters to maintain a certain temperature, etc. Fluid-tight housings rated IP67 and higher can protect the board from water and humidity. Heavy components can be fixed on the board with screws to cope with vibration.
Another option is to protect the PCB with conformal coating or encapsulation resin. Both of them are organic polymers that provide electrical insulation and offer some thermal and chemical resistance. However, their protection levels differ.
Conformal coatings are usually thin films – 25-250 microns. They conform to the contours of the PCB, thus almost not affecting the device’s weight or geometry. The minimum impact on the spacing and weight can be important for movable elements of equipment. At the same time, as conformal coatings offer a wide range of chemistry options and, therefore, protection levels, they are often used in consumer electronics as well.
Conformal coating can usually protect PCBs from standard atmospheric conditions and short exposure to chemicals and high temperatures. Such coatings cannot cope with harsher conditions, but they are inexpensive and simple to manufacture.
Encapsulation resins do not coat PCBs. Instead, a board is placed in a casing, and the liquid is poured in it to seal up the board. The thickness of this polymer layer can be 0.5 millimeters or thicker.
As a result, encapsulation (also called potting) provides much better protection, particularly from physical shock and vibration. Additionally, since the resin completely hides the PCB, it also secures the board’s design. The thickness also offers a great deal of protection against water, chemicals, and temperatures.
However, encapsulation considerably increases the weight of the device. It also makes the manufacturing process more complicated and expensive.
- Thermal management
Industrial equipment must function as long as possible without repair or replacement. Therefore, it must be heat-resistant: the higher the temperature, the faster electronic components degrade. Engineers use industrial-grade components that can withstand a wider range of temperatures, including extreme cold. If such components are unavailable or not efficient enough, one should also use elaborate cooling systems. Sometimes, combining a cooling system with consumer-grade components is cheaper than mounting industrial-grade components.
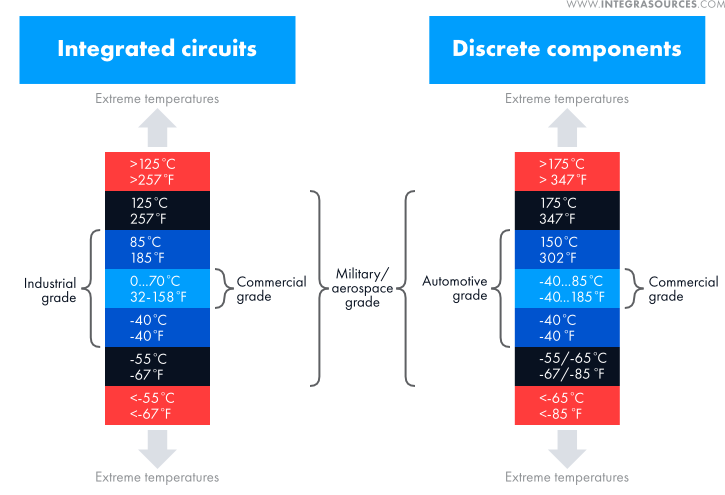
In consumer electronics, copper pads and traces are often enough to dissipate the heat. Besides, if the chip in a consumer device reaches 80C° or even 100C°, it is considered normal. But in embedded hardware development for industrial solutions, engineers would use large heat sinks, heat pipes, fans, thermal gap fillers, metal casing, and other means. Naturally, it makes devices more complicated and expensive but enhances their life span.
- Sensors and controllers
A control system consists of sensors that monitor something, a microcontroller that processes the input signals, and outputs that command the peripherals. Sensors and outputs in industrial solutions must be more reliable than their consumer-grade alternatives. Otherwise, the controller may send the wrong command making the device do something it is not supposed to. This can lead to serious malfunctions, failures, and ultimately stoppage in production.
Also, sensors must be protected from the environment. So, sometimes, they cannot be placed directly on the PCB like in consumer products. Often, the parts of the system are not integrated into a single device. Instead, they are placed at different points at the plant or factory and connected to the controller by wires or wirelessly. These are just several typical considerations to keep in mind when designing printed circuit boards for industrial applications.
Popular Industrial Electronics Solutions
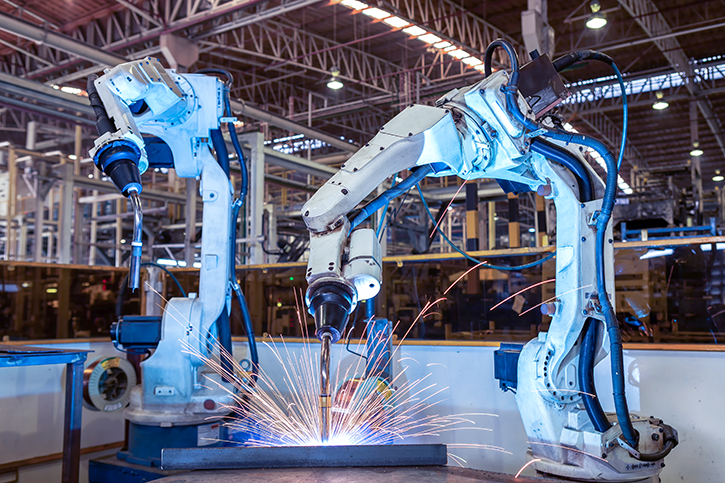
Just like any other business, industrial enterprises strive to maximize their profits and minimize their expenses. Manufacturing process development, i.e. optimizing the performance of the production cycles and manufacturing systems, often pursues the following objectives:
- Process optimization
- Energy saving
- Raw materials saving
- Predictive maintenance
To achieve these objectives, engineers use different technologies.
With the wide use of robotics in industrial automation, the need for systems based on artificial intelligence cannot be underestimated. Computer vision and optical scanners are used in quality control systems, counting systems on production lines, as well as for automated grading and sorting. AI is an integral part of solutions capable of damage recognition and assessment, automated guided vehicles (AGV) systems, etc. Voice recognition can be used in search systems, voice-controlled authentication, and navigation in vehicles. Many complex predictive maintenance and failure modeling systems utilize AI and machine learning.
The use of the Internet of Things for manufacturing simplifies the work of the personnel making it easier to gather information from different points around the plant. It is not surprising that the global industrial IoT market was estimated at $263 billion in 2021. Industrial IoT solutions allow for uniting various sensors and/or beacons into a single network. IoT is used in remote equipment and asset monitoring systems, asset, fleet, and vehicle tracking solutions, on-field workforce management, predictive maintenance, and data security. As such devices work in tandem, they also require complicated software to run properly. Read our article on industrial application development to learn more.
Augmented and virtual reality technologies can provide immersive employee training. Cloud computing allows for storing and processing large amounts of data from sensors and equipment. Various power electronics solutions including battery management and battery energy storage systems can make energy consumption more efficient.
Our portfolio includes more than 350 projects that involve IoT, AI, robotics development, and more. Many of them were industrial solutions. Contact our managers to find out how we can optimize your enterprise.
Information Required for Industrial Hardware Development
When ordering custom hardware development, it is crucial to provide the developers with all the information about the future device or system.

- Functional and other requirements
These requirements describe the functions of the future device. They allow the developers to understand what tasks the hardware must solve. It is also important to inform the team about the size, weight, and similar parameters of the device. These requirements are equally important for both consumer and industrial electronics design.
- Operating conditions
Many consumer products are not supposed to operate in harsh environments. So, unless specified otherwise, the team will take into account the requirements for standard operating conditions.
But industrial solutions always operate in non-standard conditions, so it is crucial to inform the team about them. At the very least, the developers must know about the temperatures, humidity, and vibration levels the device will face.
- Industry-specific requirements
Certain requirements may come from industry-specific standards and regulations. For example, devices used in the oil and gas industry must comply with fire safety requirements. For other industries, the team may need to reduce the electromagnetic noise coming from the hardware, etc.
- Testing and certification requirements
Any industrial hardware must comply with various certification standards and pass the corresponding tests. It is a good practice to consult a certification body to learn about these requirements before ordering custom electronics development. This way, customers can provide the team with a list of specifications and parameters the future device must correspond to.
With this information, our team can pick proper components and materials and use the most suitable design techniques so that the device complies with customer requirements and corresponding standards. It will also allow us to use the DFMA (design for manufacturing and assembly) approach to embedded hardware development and will make the work faster.
Certification and Testing
When designing new equipment, it is important to understand what certifications and testing procedures it will have to pass. In one of our previous articles, we discussed the most common certifications required for new consumer electronics. The same goes for industrial product development.
Here are some common certifications and standards industrial equipment may have to comply with:
- FCC – US national certification mandatory for devices that can intentionally or unintentionally emit RF radiation.
- CE Marking – Certification mandatory for products entering the EU market. Serves as proof that goods comply with corresponding Directives (standards in the EU), particularly the Machinery Directive, Low-Voltage Directive, EMC Directive, and many more.
- RoHS 2 Directive – Another European Directive that regulates the use of six hazardous substances in electronics.
- ASTA – International certification recognized primarily in Asia and the Middle East.
- ANSI/CAN/UL 9540 – North American standard for energy storage systems and equipment.
- UL – Mostly safety certifications for a wide range of products including certain industrial equipment.
- IECEx – International certification scheme that may be required to obtain national certification marks in certain countries.
- NFPA 70 ® - Regional standard for safe installation of electrical wiring and equipment in the US.
- ETL Mark – Proof of compliance to North American safety standards.
There are many more standards and certifications in each particular country and/or industry.
To prove that a device complies with certain requirements, one must run appropriate tests or hire a testing laboratory to do that. You can read more about PCB and electronics testing in our previous article.
Integra Source’s Experience in Industrial Hardware Design
Vibration Conditioning Device
Under this project, our team designed a device that receives vibration data from standard acceleration sensors mounted on industrial equipment. The device converts the data into acceleration, velocity, and displacement and gives these parameters out as either a 0-10V or a 4-20mA output signal. The device can serve as a part of a monitoring system for predictive maintenance.
According to Next Group Strategy Consulting, the global predictive maintenance market was estimated at $5.65 billion in 2021 and will reach $64.25 billion by 2030. That is why such projects are popular among manufacturers.
The team used STM32F4 as the MCU in the PCB design. The firmware for the MCU was written in C/C++ with Microsoft Visual Studio and Eclipse IDE. We implemented low-pass and high-pass Butterworth algorithms with maximally flat frequency response and magnitude. The team also applied infinite impulse response (IIR) filters for high-frequency filtering. As a result, the device converts even the lowest frequency signals correctly. The output signal is smooth and fully conforms to the sensor measurements. By decreasing the sampling frequency and using a processor with DSP commands, the team managed to improve the processing speed of the filters.
The device works with standard acceleration sensors and has a USB connector for interacting with a configuration console that can be run on a PC. The device also has a 4mA current source to power acceleration sensors: most of them do not have their own power sources. We also added a self-calibration function to make calibration easier and more user-friendly. Lastly, the device has an industry-standard DIN rail enclosure from Phoenix Contact.

People Tracking Device for Mining Industry
The traditional communication technologies used in location and tracking systems such as GPS and Wi-Fi do not work well underground. So, our customer, who works in the mining industry, required a solution that could overcome these limitations. He also asked us to make the system energy-efficient.
We developed a gateway device which miners can wear on their belts. The team used nRF52832 with BLE 5.0 support and Cortex-M4F core as the MCU for the device. Certain areas in the mines are supposed to be equipped with Bluetooth beacons. The device can capture the signals from the beacons and calculate the distance based on the signal power.
Then, it transfers its identifier to the cloud server using Wi-Fi. If Wi-Fi is lost, the device uses 3G. It has an SIM5360 module responsible for 3G communication. The module can also connect to GPS if there are no beacons nearby.
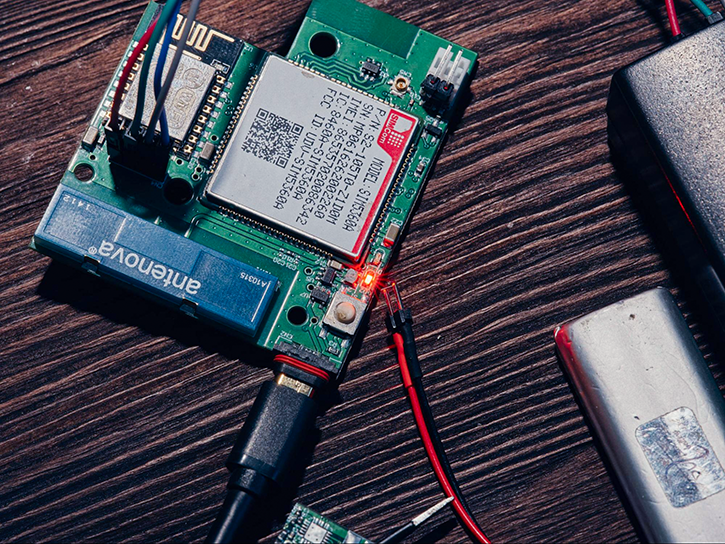
This allows for monitoring the location of miners underground with an accuracy of up to 1 meter. The accelerometer in the device monitors the miners’ activity, allowing the management to gather statistical data and improve the safety of the personnel.
We used Microsoft Visual Studio and the Visual GDB plugin for the firmware development which was written in C/C++. The device can work for 7 days on a single charge and is placed in an IP67 waterproof case.
Customizable Asset Tracking Platform
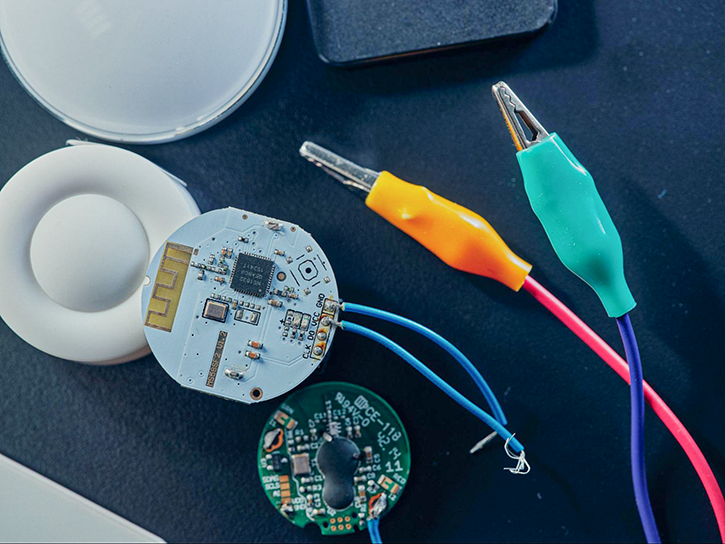
Commercial and industrial customers often require asset tracking solutions. So, our team decided to design a customizable device pre-equipped with basic asset-tracking functionality. The solution can be customized for particular business goals, which reduces the development time by 40-60%.
The system consists of a GPS tracking device and a cloud platform for storing and displaying the data on iOS and Android devices in real time.
In this project, the team used STM32L452 with Cortex-M4 core as the MCU. We managed to make it very small – 40x40x6.8 mm without housing and battery. It can be attached to assets or simply kept in pockets. The device is equipped with temperature and humidity sensors, an accelerometer, a gyroscope, and GPS. Thus, it can monitor both the location and the condition of the assets. Therefore, the system is suitable for tracking a variety of asset types including people, vehicles, containers in a warehouse, and equipment in a factory, making it useful for commercial and industrial applications.
The device transmits the gathered data to the cloud server via Bluetooth, Wi-Fi, or GSM. The tracker has BLE, Wi-Fi, and GSM/HSPA communication interfaces. For indoor positioning, the server calculates the distance between the device and beacons based on the power of the signals. The tracker is also equipped with an SD Card that stores the location and sensor data.
The accuracy of the device is up to 1 meter. It can also work for 1 month on a single charge.
Conclusion
The use of robots for manufacturing, artificial intelligence, industrial internet of things hardware, and other technologies help enterprises to attain various manufacturing process development objectives. They allow manufacturers to monitor different assets, resources, and equipment to make informed decisions. Industrial automation solutions exclude or minimize the human factor in manufacturing, assembly, and quality control. That is why industrial electronics and IT solutions for the manufacturing industry are in demand.When it comes to industrial hardware development, the designers must take into account the strict requirements applied to such equipment. They include higher reliability, strong protection from environmental hazards, more efficient heat dissipation, etc. Our engineers have completed more than a few industrial projects, so we know how to design embedded hardware that will improve any enterprise. Contact our team to discuss how we can help yours.
Share this article
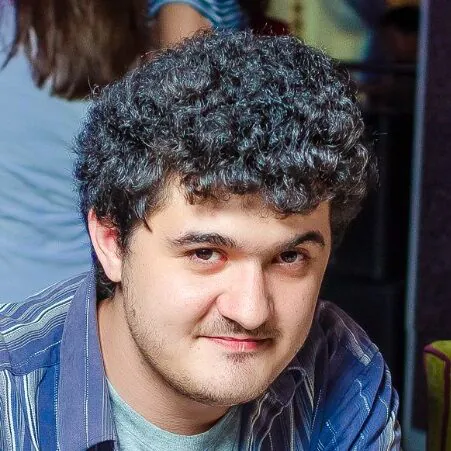
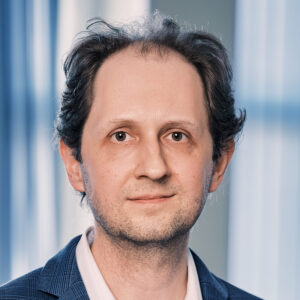
Related
materials
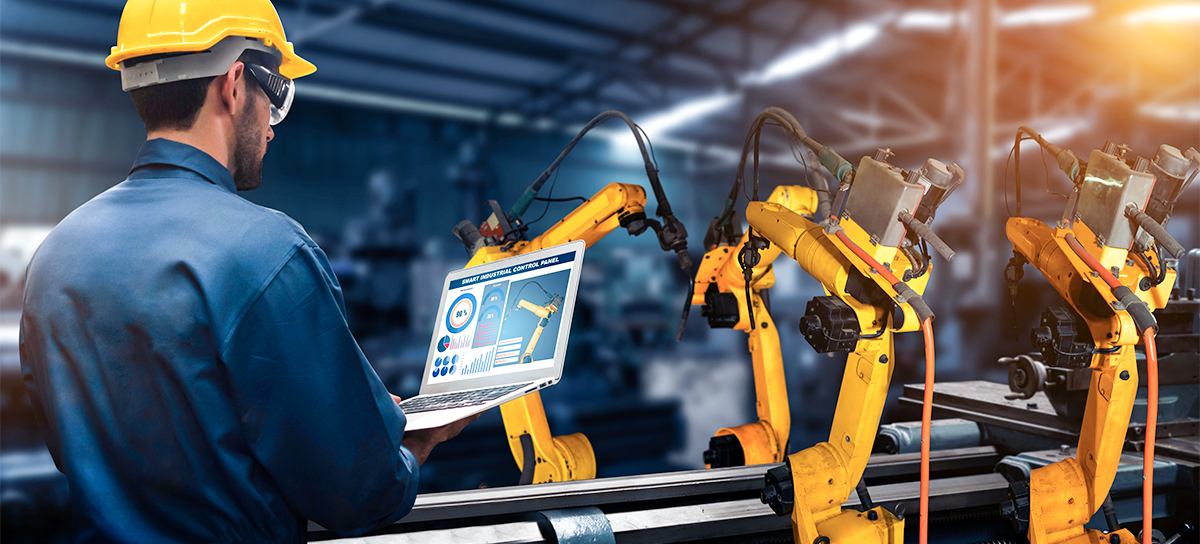
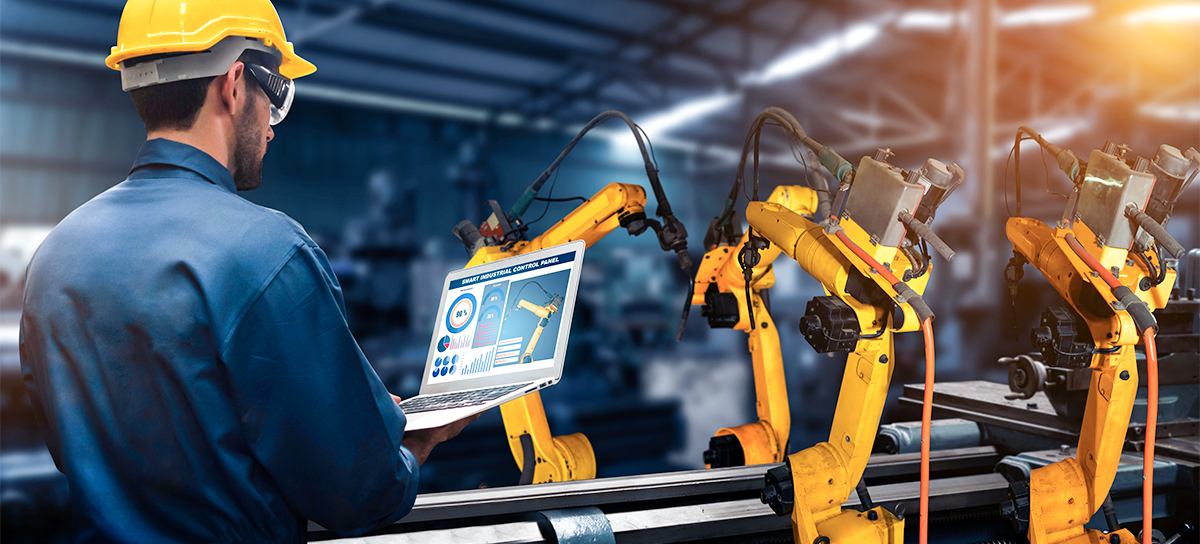
Industrial App Development: A Silver Bullet to Wipe Out Manufacturing Challenges
Software for industrial solutions is unique in its functions and characteristics. Cross-platform features allow employees to monitor production processes from...
LEARN MORE
LEARN MORE
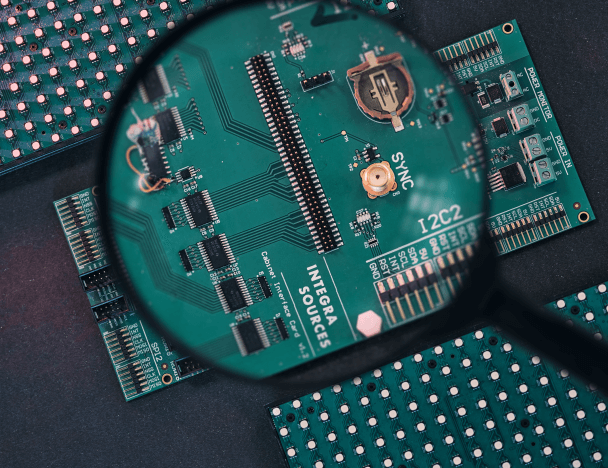
PCB and Electronics Testing Before and During Manufacturing: Importance, and Methods of Implementation
Find out how PCB designers and manufacturers test circuit boards before and during production and why these actions are so...
LEARN MORE
LEARN MORE
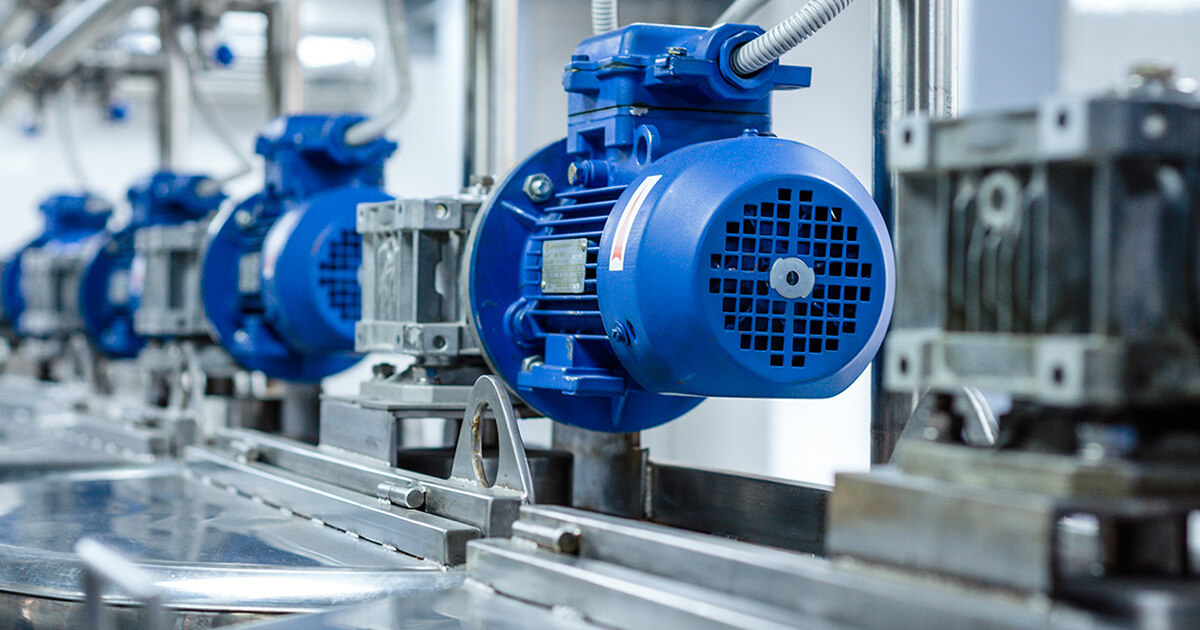
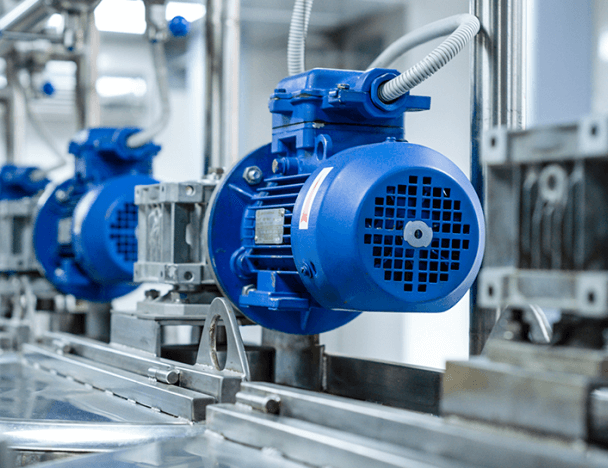
Vibration Conditioning Solution for Industrial Automation
The solution measures industrial machinery vibration. We implemented analog and digital filters that make the output signal smooth and strong.
LEARN MORE
LEARN MORE