This website uses cookies so that we can provide you with the best user experience possible. Cookie information is stored in your browser and performs functions such as recognising you when you return to our website and helping our team to understand which sections of the website you find most interesting and useful.
Vibration Conditioning Solution for Industrial Automation
We at Integra take part in the development of various industrial solutions. We are keenly interested in such tasks because they often require an unconventional approach and help us extend and upgrade our technical competence.
More recently, we see a growing demand for a transition from analog products to their digital versions. In one of our latest projects, we developed a digital variant of a vibration conditioning device for industrial automation. Our deep experience in digital signal analysis really came in useful for this project.
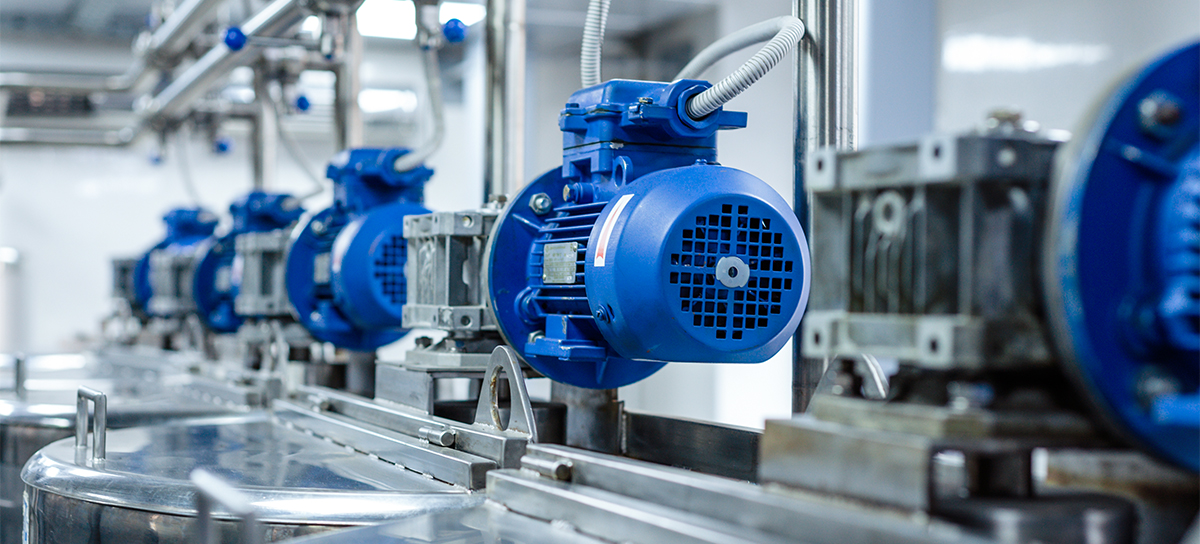
Request
Our customer, who was engaged in motorsports electronics and industrial automation solutions, decided to create a device that reads acceleration from a standard industrial sensor, transforms it to different values (acceleration, velocity, or displacement), and gives these values up to the outputs. The device was supposed to be developed from scratch.
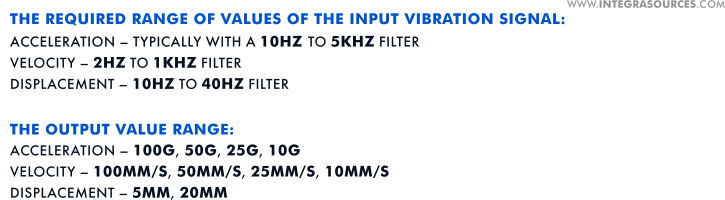
Solution
We designed a vibration conditioning device that receives data from a vibration input sensor mounted on industrial equipment such as a gearbox, a fan, or even a pump. The device converts the data to the required values (acceleration, velocity, or displacement), and gives the converted values out as either a 0-10V or a 4-20mA output signal.
The device has an LED, which indicates if everything is fine with the input signal from the sensor. The device is also equipped with an additional output that repeats the input signal either as-is or without the DC component.
Writing firmware for the MCU, we implemented high-pass and low-pass Butterworth filtering algorithms that have a maximally flat frequency response and magnitude. For high frequency filtering, we also applied infinite impulse response (IIR) filters.
These filtering algorithms provide a smooth input signal integration. We managed to improve the processing speed of the filters by decreasing sampling frequency and using a processor with DSP commands.
We met all the requirements for the values of both the input and output vibration signals. Our solution makes it possible to transform the input vibration signal correctly, even at the lowest frequency value, and achieve the required accuracy.
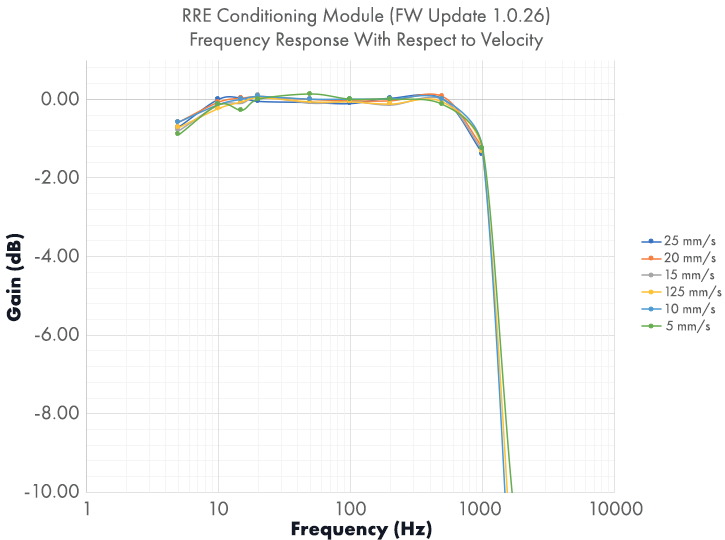
Main Challenges Solved
One of the main challenges related to the hardware design was to make a stable 4mA current source for the vibration sensor power (in case it was not powered by an external source). We had to test several circuits before we got the final solution, which provides stable power without noises that influence the measurements of the sensor.
The other challenges of the project related to its usability, so our goal was to make the device more user-friendly. For example, we added a self-calibration function that simplifies the calibration process for the user to the greatest possible extent.
We also optimized the output mode switching for both current and voltage. This mode is set via the console interface with no hardware modifications.
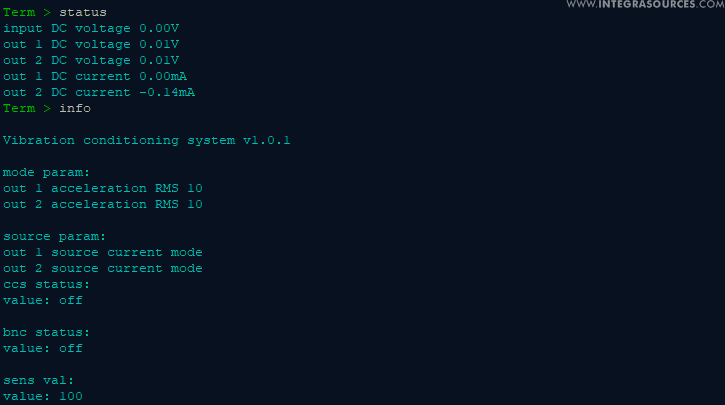
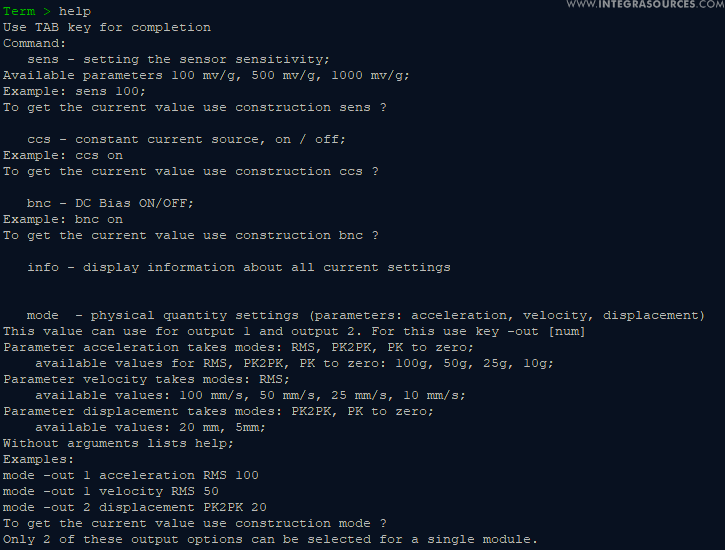
Scope of Work
We completed the design of both hardware and firmware for this solution.
Embedded hardware development
- schematics design;
- PCB design;
- preparation of production files and documents for the manufacturer;
- prototype assembly;
- hardware testing;
- debugging.
Firmware development
- data acquisition;
- digital filtering;
- data processing;
- output signal generation;
- self-calibration;
- UART configuration.
Technologies Used
- This project is closely connected with digital signal processing.
- We used an STM32F4 as the MCU for the device.
- The device is equipped with analog filters.
- We designed the device configuration console.
- The device is able to generate 0-10V and 4-20mA output signals.
- We added the self-calibration feature to the device.
- The device works with a standard acceleration sensor.
- The acceleration sensor can be powered by either an external power supply or a stable built-in 4mA current source.
- A sufficient part of the development was connected with voltage/current meters.
- The device has a USB connector to interact with the device configuration console running on a PC.
- We used Microsoft Visual Studio and Eclipse IDE for firmware development.
- The firmware was written in C/C++.
Result
We developed solid hardware and firmware solutions that fully met the initial requirements. The prototypes of the device tested by our QA department and the customer showed great results.
The device can provide stable power for the acceleration sensor if needed. The signal from the sensor goes through several analog and digital filters. That makes the output signal smooth and 100% corresponding to the measurements of the sensor.
Outputs of the device are configurable via the console - they can form acceleration, velocity, or displacement (RMS/peak-to-peak/peak) values converted from the input signal to a standard 0-10V or 4-20mA signal.
Users can easily monitor the state of the input signal - the green light of the LED shows that everything is fine. In case any issue arises, like wire damage, etc., the user will see the red light.
The device has an industry-standard DIN rail enclosure from Phoenix Contact.
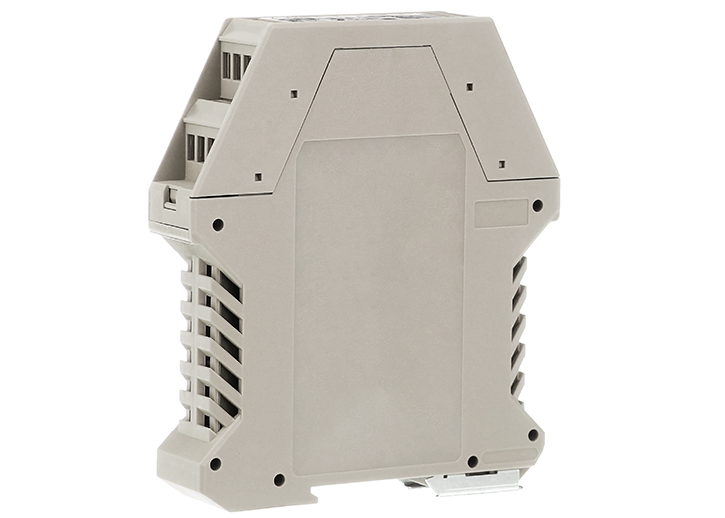
After the successful completion of the project, we continued the cooperation and created a cost-friendly light version of the device with limited functionality.
Integra Sources delivers to the highest standards, not only in the physical work they produce but also in their communication and documentation. It has by far exceeded our standards. They researched the project in-depth to better understand our goals - that really impressed us.

Output signals generated by the device
Correspondence of the output signal to sensor measurements
You might also like...
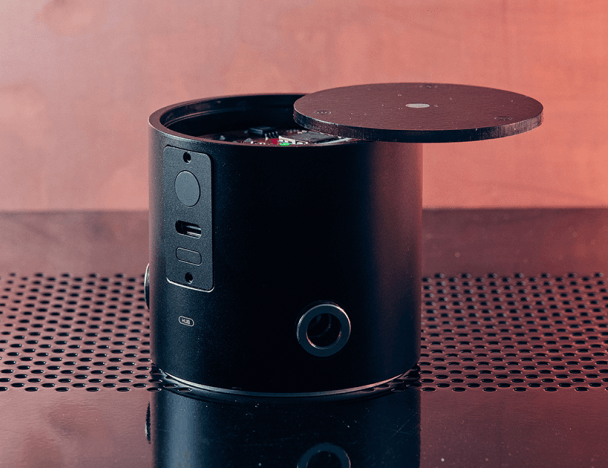
IoT System Development for Manufacturing Reinforced Composites
The IoT device detects leaks on a vacuum bag and communicates this information to the user via a phone, tablet or PC.
LEARN MORE
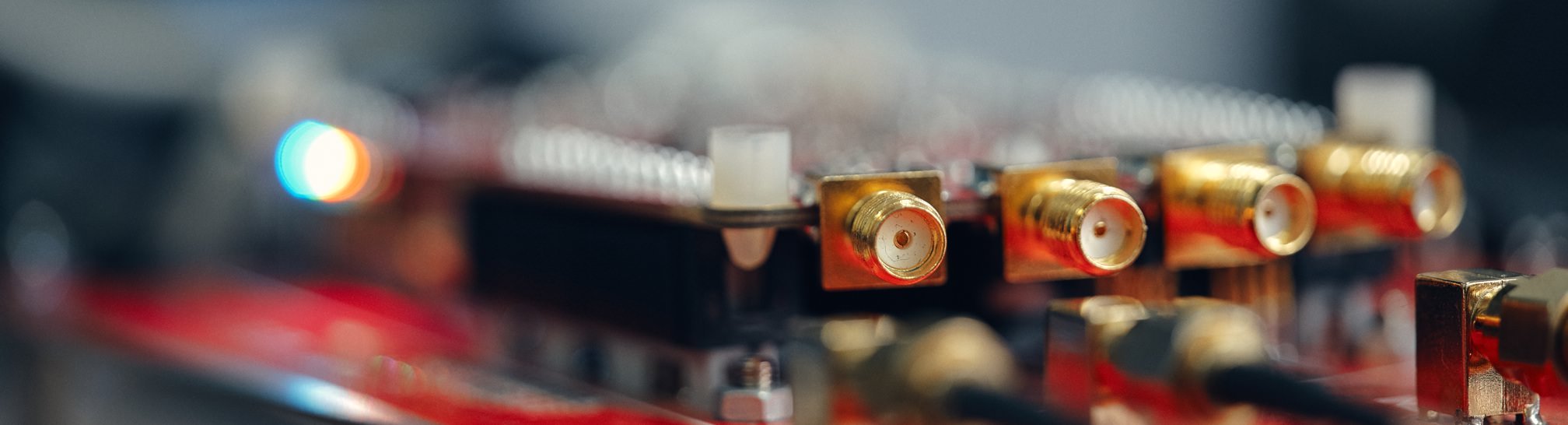
A Client-Server System for Test & Measurement Applications
We developed a licensing mechanism for the test and measurement platform and apps including a spectrum analyzer and an oscilloscope that can be accessed from a web browser
LEARN MORE